Talking to users and learning more about their experiences.
Next generation low-cost prosthetics
Amputees are often excluded and isolated due to bodily limitations and societal stigma. Prostheses can help them to live more independent, healthy and active lives and lets them be part of the society with lesser limitations. However, access to these devices is extremely limited, and even when they are accessible, prostheses are often not accepted. The industry today focuses on high-tech products, while simpler, more affordable solutions are being mostly neglected. In this project, I tried finding ways to improve accessibility, functionality and acceptance. I did this in close collaboration with users, stakeholders and my collaborating partner Agile Robots. The final concept combines advantages of both electric and mechanical prostheses in a low-cost, open source design. It allows for ergonomical, functional and aesthetic customization based on the users’ individual needs and desires. This process is facilitated by leveraging technologies such as 3D-printing to reduce cost and manual work effort.
Project Information
This project is about challenging recent developments in the industry for upper limb prosthetics. I wanted to look into prosthetics because it is a societal relevant topic that is placed at the intersection between mechanical engineering and wearables designed for humans. Highly individual requirements in terms of functionality and appearance, as well as several other factors such as lack of specialised healthcare infrastructure make it a very challenging product category. I started into this project with the goal of exploring ideas for improving accessibility, functionality and acceptance of these devices. I am convinced that designers can have an impact by approaching this highly engineering-driven topic from a fresh and also critical human centered perspective. The project was done in collaboration with the design team of Agile Robots, who supported me throughout my project journey.
Methods
In my research, I looked at the topic from various stakeholder angles: the amputees, the clinical prosthetists, the orthopedic technicians, education and researchers view. The reason why I did this is that such a health-critical product cannot be designed without insights from all perspectives. I conducted both online interviews and on-site visits to hear from the stakeholders themselves and see the way the interact with prosthetic devices. Since technological advancements have always had an impact on the field of prosthetics, I also looked at recent developments in manufacturing, material technology and AI through desktop research. With this broad understanding as a background, I explored various ideas that concerned not only the device itself, but the whole process before getting a prosthesis as well. I stayed in conversation with the various stakeholders over the remaining concept development process and continuously assessed and validated the potential of my ideas.
Result
The final design concept combines advantages of both modern electronic systems and traditional body-powered prostheses into a lightweight and robust solution, that can be used with a range of inexpensive, terminal device modules to provide users with individual benefits. By using available technology like 3D-scanning, procedural configurator softwares and a new way of 3D-printing, the prosthesis can be tailored to the individual user while reducing costs and manual work effort.
The prosthesis is cable-actuated by body power using a breathable undershirt that is locally reinforced to equally distribute the pulling forces. The shirt can be comfortably worn underneath regular clothing, and the prosthesis can be conveniently connected and disconnected from it depending on the users’ needs. Using body power eliminates the need for heavy batteries and motors and lets the users control the prosthesis in an intuitive and fast way.
The direct connection to the body also creates natural feedback for the gripping force. A small electronic lock-switch can be triggered using a myoelectric signal from the residual limb. It locks the hand’s grip, which makes it easy to move around with a grasped object. It can then be unlocked using the same signal again. The small amount of needed energy for the switch can be harvested from the users’ natural motion, and only little weight is added to the prosthesis.
The prosthesis can also be switched to an idle mode, where the user can move around freely without making unwanted movements. The structure consists of an inner rigid part that connects to the wrist with a tube, and a flexible outer socket. When passively turning the wrist, the socket deforms with the movement, which creates a natural form-transition between the arm and the terminal devices. The outer socket is covered by a soft layer of fabric, which further improves the look and feel of the prosthesis. It is also an element that allows for easy customisation. The hand is simplified to perform the three most used grips in a reliable way, while keeping the design simple and friendly in its appearance. The thumb can be passively switched between the positions. The whole hand contains no special components and can therefore be cleaned using a washing machine or even a dishwasher.
Heinrich Zaunschirm
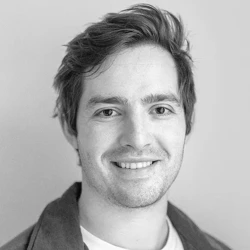
In collaboration with:

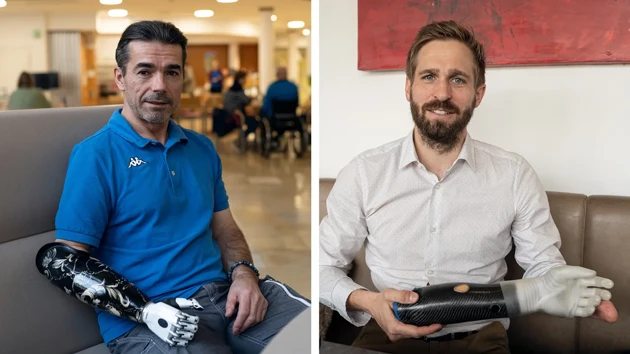
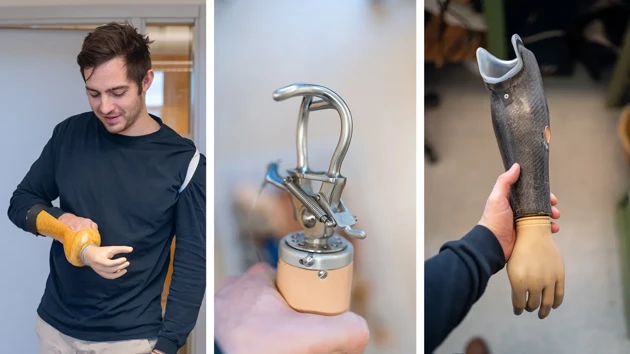
Trying a body-powered prostheses and getting a feeling for existing products.
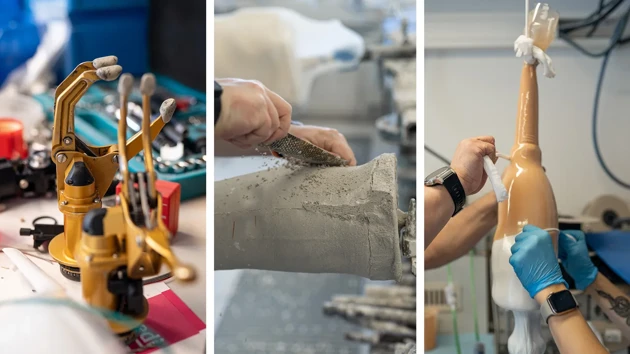
Visiting prosthetists and orthopedic technicians to get a better understanding of the whole process.
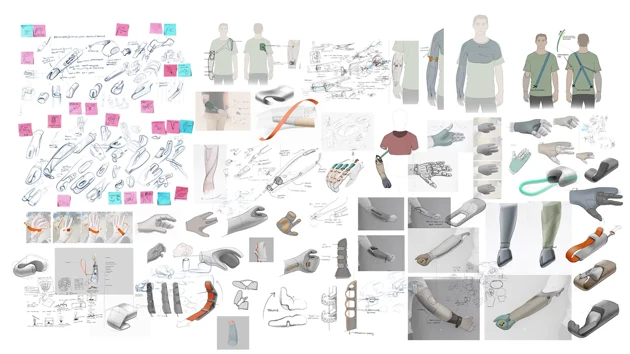
Sketch exploration.
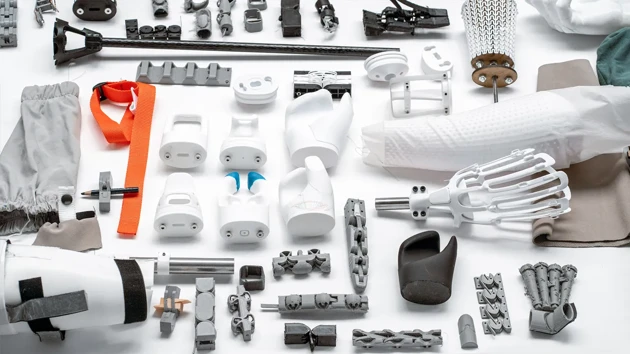
Prototyping.
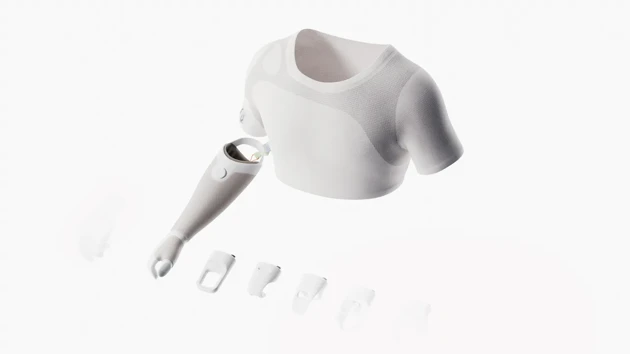
The final concept – a hybrid, body-powered prosthesis.
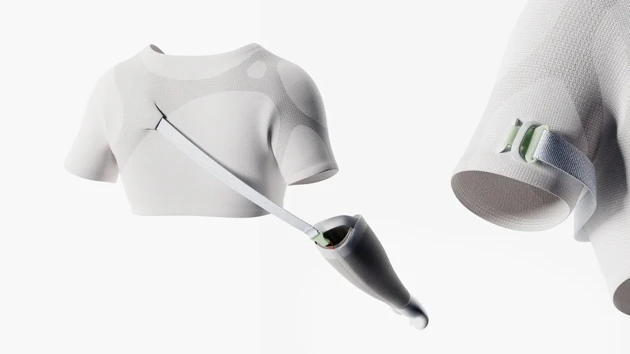
Locally reinforced harness undershirt with strap.
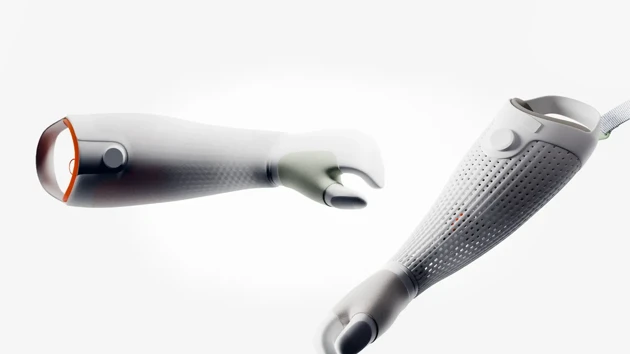
Underlying flexible, shape-changing structure.
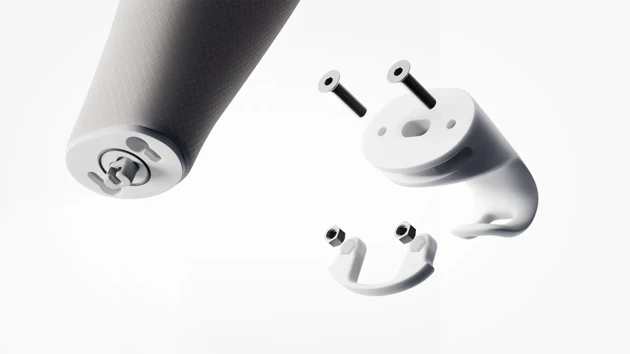
Simplified, low-cost bayonet fitting for attaching simple, 3D-printed terminal devices.
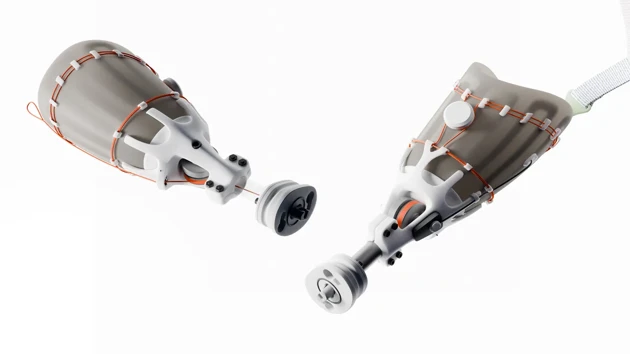
Inner structure and package with tightened silicone socket, electronic switch and cable transmission.